Our experienced team has developed a comprehensive package of liquid and powder cementing additives, carefully designed to ensure wells have a protective barrier against fluids flowing through the formation.
With a huge amount of variability in this type of chemical technology, as well as an increased demand for traceability and sustainability, we caught up with our cementing expert, Mike Morrice, asking him to shed some light on the changes and challenges of this process…
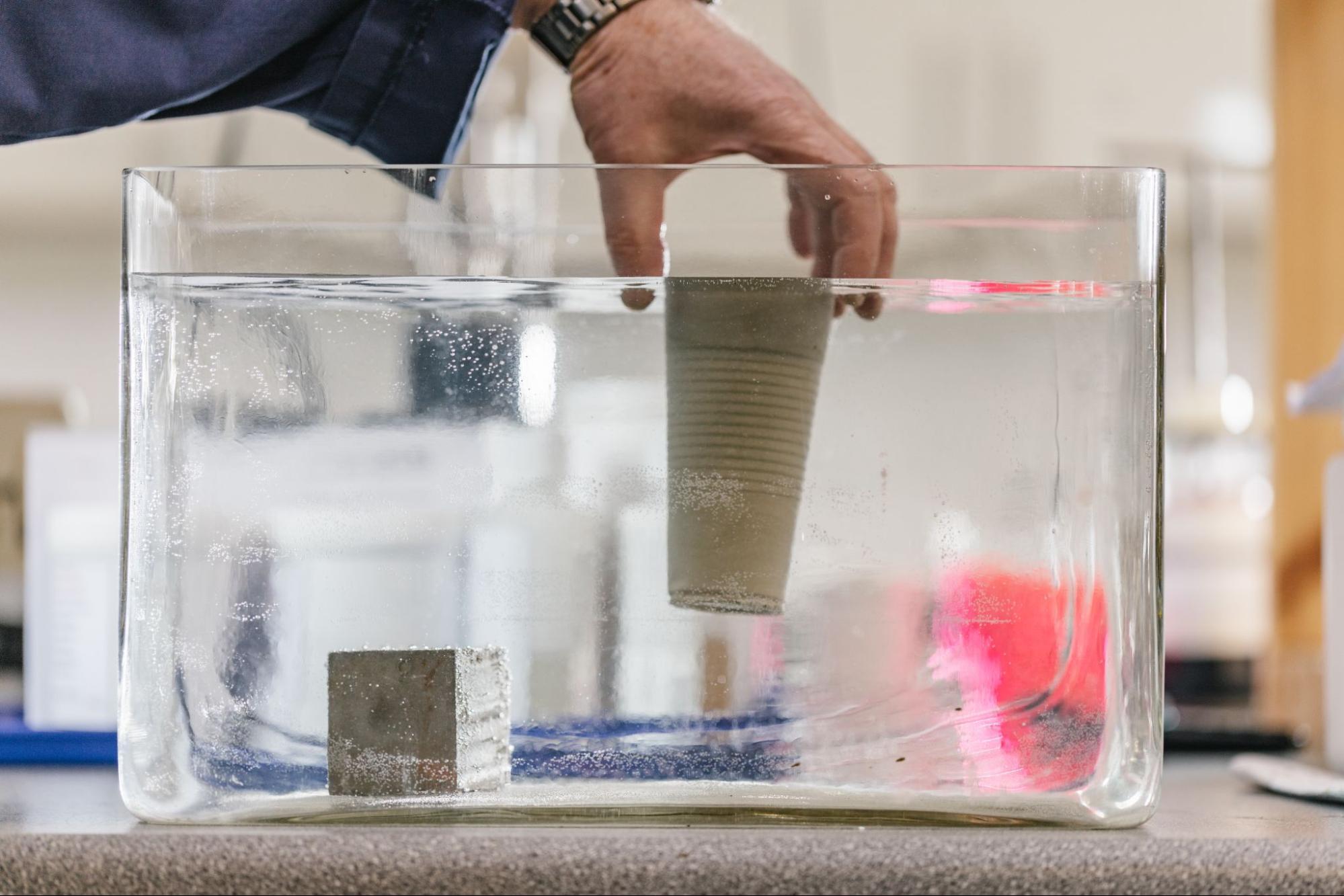
What is cementing, and why are cementing additives used?
“Cementing is the process by which you combine a cement slurry, additives and water, then pump this mixture into various annulli surrounding the casing or in the open hole. This provides an effective barrier to potentially corrosive well formation fluids , and bonds the casing to the formation.
“Most cementing jobs will have different parameters that need to be met, whether it’s the compressive strength, pump time, rheology, fluid loss or slurry density, all of which can be manipulated using different additives in the cement slurry.
“Cementing additives can include accelerators, which shorten the thickening time of the cement, as well as retarders, which do the opposite and make the cement thickening time longer. They can also decrease or increase the density of the cement and transform the compressive strength and mechanical properties of the cement, as well as flow properties and dehydration rates. Extenders can be used to increase the yield of the cement in an effort to reduce the cost of cementing, and antifoam additives can be added to prevent foaming within the well, while bridging materials can be added to plug lost circulation zones.
“A lot can be done with the use of cementing additives, however, your cement should be quite straightforward so we typically avoid using a large suite of additives, unless required. This is because additives impact each other differently depending on what is used in the formulation, so if an additive isn’t required then we don’t put it in - it’s better to try and test methodically, and step-wise until all parameters are met.”
How has cementing changed over the years?
“One of the biggest game changers when it comes to cementing was the Deep Water Horizon disaster. There were a lot of little things that combined to make this a major incident, and this has totally changed the way that cementing jobs are carried out. Traceability, lab qualification and quality assistance have definitely become more crucial in the wake of the Deepwater Horizon disaster.
“The crash in the oil industry would be another huge change we’ve seen over the last 10 years. Due to cost cutting, many companies have lost skills and experience in their team, and cementing has definitely been an area impacted by this. We can see a gap in the industry in terms of in-house cementing expertise, and have had many companies approach us to benefit from our deep level of knowledge, laboratory capability and experience in this area.”
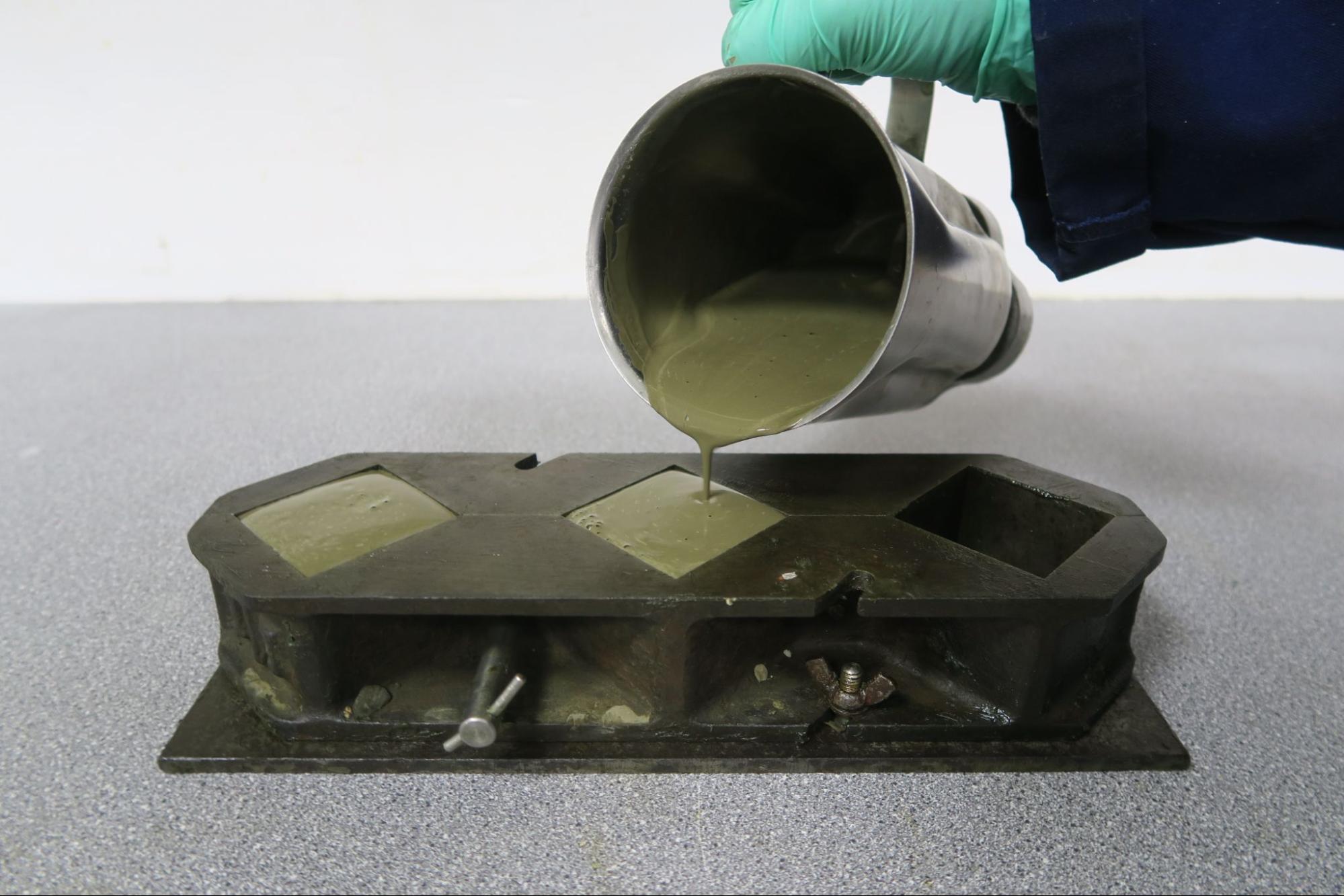
What challenges are faced when it comes to cementing?
“Compatibility between different additives can be a challenge to solve, but this is where testing comes in - all pre-job testing should be performed with the cement and additives to be used on a specific job, so you can fine tune the slurry design well beforehand.
“Issues on site can be huge if you haven’t done the correct testing first. For example, if your cement sets too early or too late, or it’s unpumpable into the well, then that could delay a whole operation and production, and that asset might have to shut down while you deal with integrity issues you weren’t expecting, which will be extremely costly.
“Although we test our products rigorously, if you’re dealing with a really old or problematic well and don’t have a working temperature of it, for example, then that takes some of the certainty away. What you then have to do is try to work out the temperature based on depth, which can be quite reliable but occasionally, it can mean there’s an element of trial and error.
“The quality of cement has and is continuing to change over time which can also be challenging, because although the cement you’re using may be recognised as American Petroleum Institute cement, it can still have quite a bit of variability in it. Raw material supply for cement has massively changed over the last decade as the industry tries to become a bit greener. A big part of cement is fly ash which comes from coal power - you can imagine the amount of coal power stations that have shut down in the UK and Europe over the last few years, so the variability of cement then changes because the source of that raw material is different.”
How do you overcome some of these challenges?
“Having accurate and in-depth information makes it a lot easier to qualify a cementing product. If a customer estimates the temperature the product needs to work at but it turns out it’s something different, that could considerably change the percentage of an additive used or the additive that is required for the job.
“Understanding what equipment the customer is using to mix the cement or how they are going to mix it also helps us massively. Some people do batch mixing of cement, whereas others mix it ‘on the fly’ when it’s needed. Some people blend additives into the powder of the cement rather than mix it with water. It’s important that we know what’s going to happen once the product is supplied to the customer because if there are other additives in their mixture that we don’t have sight of, or it’s being mixed using a different method, it can have a detrimental effect on our products.
“Being able to fully supply the entire mixture is really beneficial for us and means that any potential issues around compatibility and traceability are minimised. We can test the products together and have full visibility of what is being mixed together.”
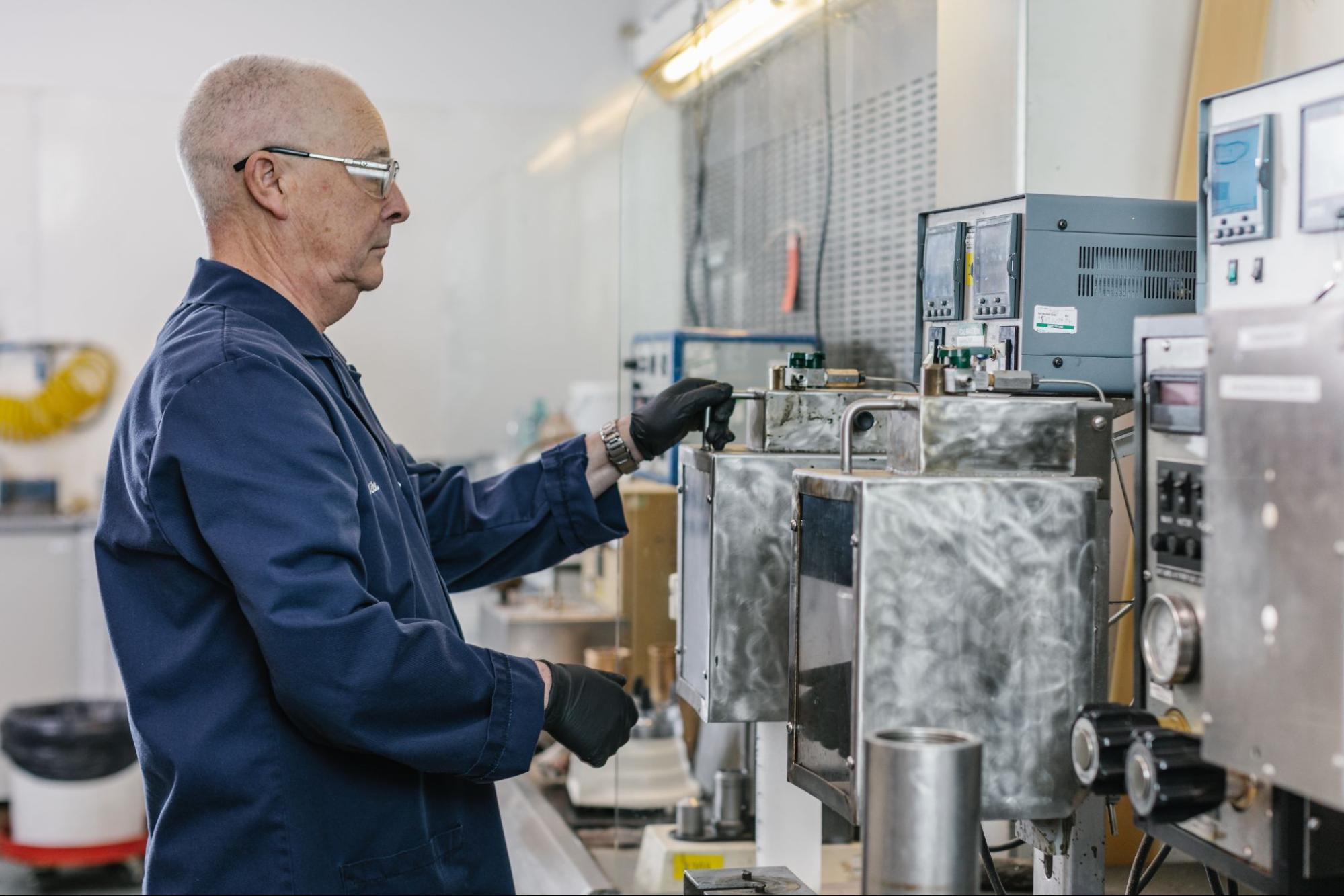
What do you think the future of cementing will look like?
“As the world moves more towards sustainability and environmentally friendly practices, the properties of cement will continue to change. Going forward, you might need to look at using alternative additives, which could result in cement that has a higher or lower sensitivity to retarders, or a lower tendency to gel with polymer additives, for example.
“We’re currently being approached by some industry bodies to look at qualifying and producing cement designs that would have better long term integrity. There has been a real focus on responsibly operating in the North Sea in particular, but people want to be able to do that economically. As a result, they might want to reduce the volume of cement they are using, in order to reduce the quantity of carbon intensive cement but still have that same level of integrity.
“At the moment we’re looking at creating some specialist additives, with some exciting projects we are hoping to get funding for, as well as some really new initiative materials for the future.”