There are an abundance of reasons why regular pigging is advantageous - from cleaning out debris, water or oil, to executing preventative or corrective maintenance to ensure the integrity of a pipeline.
Pigging is also often used in the pre-comissioning or decommissioning phases of a pipeline to prepare the line to receive oil or gas by removing the pre commissioning fluid (usually water) and replacing it with gas or glycol based fluids, or in the case of decommissioning, cleaning the line of hydrocarbons and debris to allow it to be decommissioned.
However with these benefits come an array of challenges associated with both mechanical and foam pigs, which are the most commonly used types, that can result in costly problems or prevent pigging from happening at all.
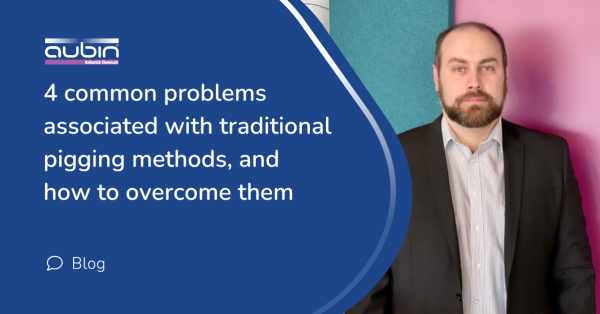
In this blog post, Adam Brown, Technical Sales Manager for Global Pipeline Business, discusses these common issues and why they occur, as well as a potential solution for overcoming them.
COMMON CHALLENGES MANY TEAMS FACE WHEN USING MECHANICAL OR FOAM PIGS:
1. Unsuitable for some pipelines
“Although mechanical and foam pigs are the go-to options, they are actually unsuitable for many pipelines. They cannot be used to pig subsea flow lines or flexible flow risers, or pipelines with corrugated walls or u-bends.
“Looking specifically at foam pigs, although they can be deformed, they do not have the capability to “spring back”. This makes them a poor choice for variable diameter or flexible flowlines, which have a corrugations or a helical internal surface, and will reduce the effectiveness of the pig to the extent that it may result in fluid bypass and the pig getting stuck.”
2. Can get stuck in the pipeline
“Mechanical pigs in particular pose a high risk of getting stuck if they are deployed in unsuitable pipelines, or if there is a build-up of debris.
“The general design of mechanical pigs can also result in them getting stuck. Often, fluid can go over the top of the pig, which can slow it down and stop it moving altogether.
“A stuck pig is a big worry for pipeline operators. In some cases, it can:
Restrict production
Act as a place for wax, scale or hydrates to form
Prevent regular integrity inspections using “smart” or intelligent pigs
"The pig will ultimately need to be removed, and this may require extensive pumping and flushing to dislodge the pig, cutting open the line or even the construction of a new piece of pipeline to bypass the pig. Such activities require operators to stop production and make the line safe. It's very expensive and something nobody wants to happen.”
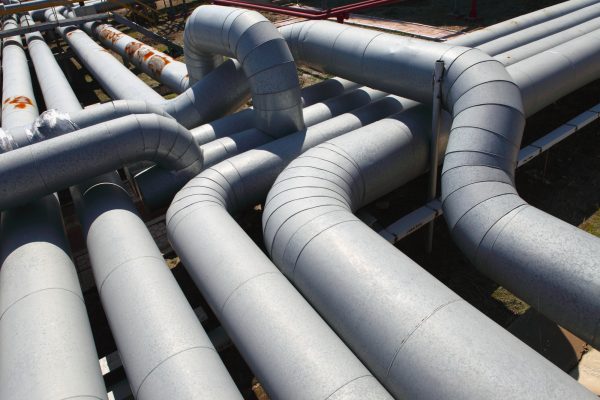
3. Inability to navigate varying diameters or sharp bends
“The ideal pipeline for mechanical pigs, and to some extent foam pigs, has a continual single diameter, with no changes or no sharp bends.
“But in reality, not many pipelines are like this. Most have diameter changes, even of the slightest degree, as well as bends and other complex areas that must be navigated by a pig, if pigging is to be done effectively.
“Even foam pigs, which many perceive to be much more flexible than their mechanical counterparts, have to be supplied to the exact size of the pipeline, which makes them less effective overall.”
4. Pig launching facilities are required
“The final challenge many companies face is not being able to run their chosen pig, as they have no way of deploying it.
“If you have no launching or receiving facilities, your pigging is not possible with these traditional methods. And it can be a considerable expense to add them on to your pipeline - this can cost hundreds of thousands or even millions of dollars.”
A SOLUTION FOR OVERCOMING THESE PIGGING CHALLENGES:
There is a solution to overcoming the above pigging challenges, that many companies don’t know about or have never tried: gel pigs.
Using newer technology, gel pigs are designed to do what traditional pigs can do, and much more. In a nutshell, gel pigs can:
Be launched with no pigging facilities
Navigate varying diameters and bends
Maintain a good seal over long distances
Pig traditionally unpiggable pipelines
Be removed from subsea lines by displacement through a small valve or opening at the subsea wellhead
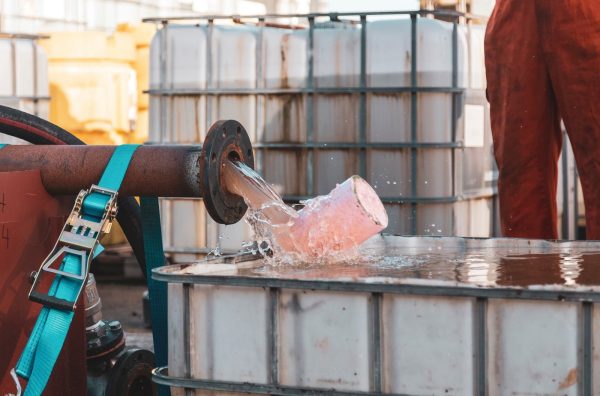
Here at Aubin, we have developed a range of highly effective gel pigs to enable companies to regularly conduct effective pigging, and avoid these common challenges. And the success we have seen has been fantastic - with so much positive feedback from our customers.
Our EVO-Pig range has been developed in our in-house laboratory in Aberdeenshire, to withstand varying pressures and temperature to suit our customers’ needs. We can also tailor our gel pigs too, for specific requirements.
A TOP TIP FOR SELECTING THE PERFECT PIG
Adam says: “My key piece of advice for anyone researching suitable pigging methods, is to explore alternatives.
“So many people simply do things because that’s the way they’ve always been done - but technology is advancing all the time, and new opportunities may exist for you to get even better results for your company.
“Determine what your are trying to achieve and the purpose of your pigging, then weigh up the pros and cons of all available solutions. Which method comes out on top in terms of being able to complete the job effectively and efficiently?”
If you’d like to discuss your pigging requirements with the Aubin team, we’d love to hear from you. Either send us a message by completing the form below, or learn more by visiting our EVO-Pig page.